Part F Domestic Ventilation Guidance
Overview
In this report an outline of the two most common and easy to install systems of ventilation will be given, with a view to guide any developer making a choice on which to install into their properties.
A broad description of the systems will be given, the pros and cons of each system will be shown for comparison and the methods of compliance will be explained with reference to Building Regulations Part F.
Systems of Ventilation
Adequate ventilation is essential in maintaining a healthy environment. It prevents the build-up of excess levels of humidity, which can lead to condensation, mould and can consequently result in health issues. Adequate ventilation also provides air for fuel-burning appliances, such as wood burners and removes cooking smells.
There are 4 main systems of ventilation with a fifth for more complex applications, but the most common two are System 1 and System 3. According to Building Regulations Part F, systems of ventilation cannot be mixed without prior consent from Building Control.
In both cases, solid duct and simple low resistance grills on the outside are always recommended as they offer lower air resistance and aid compliance. It is highly recommended that gravity shutter grills and roof tile vents are avoided as they are generally highly resistive to air flow.
System 1 Background ventilators and intermittent extract fans
System 1 is the most common type of ventilation installed with the simplest compliance targets.
As can be seen with the targets in Table 5.1a, a single fan is required in every wet room including any Utility room where there is provision for sinks, washing machine or dryers.
Where there is no cooker hood, an extractor can be fitted adjacent to the cooker which achieves 30l/s, or an extractor anywhere in the kitchen which reaches 60l/s.
There is a requirement from Building Regulations Part F for background ventilators such as trickle vents or passive ventilation sized appropriately for the size of the plots. This can be derived from table in section 5.2a of Building Regulations Part F. In most cases, trickle vents installed into each window frame will suffice.
Specifically, Decentralised Continuous mechanical extracts can be installed in a similar manner to System 1 fans, with the exception that they run continuously. These are more common in plots where the air tightness result is expected to be below 3m3/h/m2.
As shown by cross referencing Tables 5.1a and 5.1b taken from Building Regulations Part F, compliance is achieved by each individual fan reaching its “Minimum high rate”, and for the total of the low rates to be greater than the “whole dwelling ventilation rate”, which must be calculated prior to installation to ensure compliance can be reached by the fans.
Ventilation Testing and commissioning requires that the low and high rates of each fan be taken, then adjustments to be made to ensure that the flow rates are reached. This process can often lead to excessive noise from fans in situations where insufficient fans have been installed, requiring that a number of fans need to be run at higher speeds continuously.
Cooker hoods may be installed but cannot be ducted externally, instead made to recirculate the air back into the kitchen allowing a System 3 extract installed in the kitchen to remove the polluted air.
For any design air permeability, controllable background ventilators having a minimum equivalent area of 2500mm2 should be installed in each room, except wet rooms, from which air is extracted. As an alternative, where the design air permeability is leakier than 5m3/h/m2 at 50Pa, background ventilators are not necessary but see precautionary advice in paragraph 5.10 of Building Regulations Part F as this approach can lead to long term issues.
Ashby Energy Assessors Blog and News
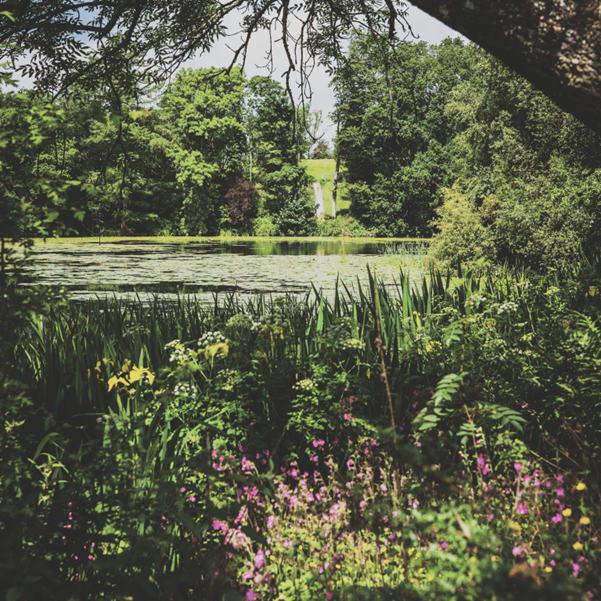
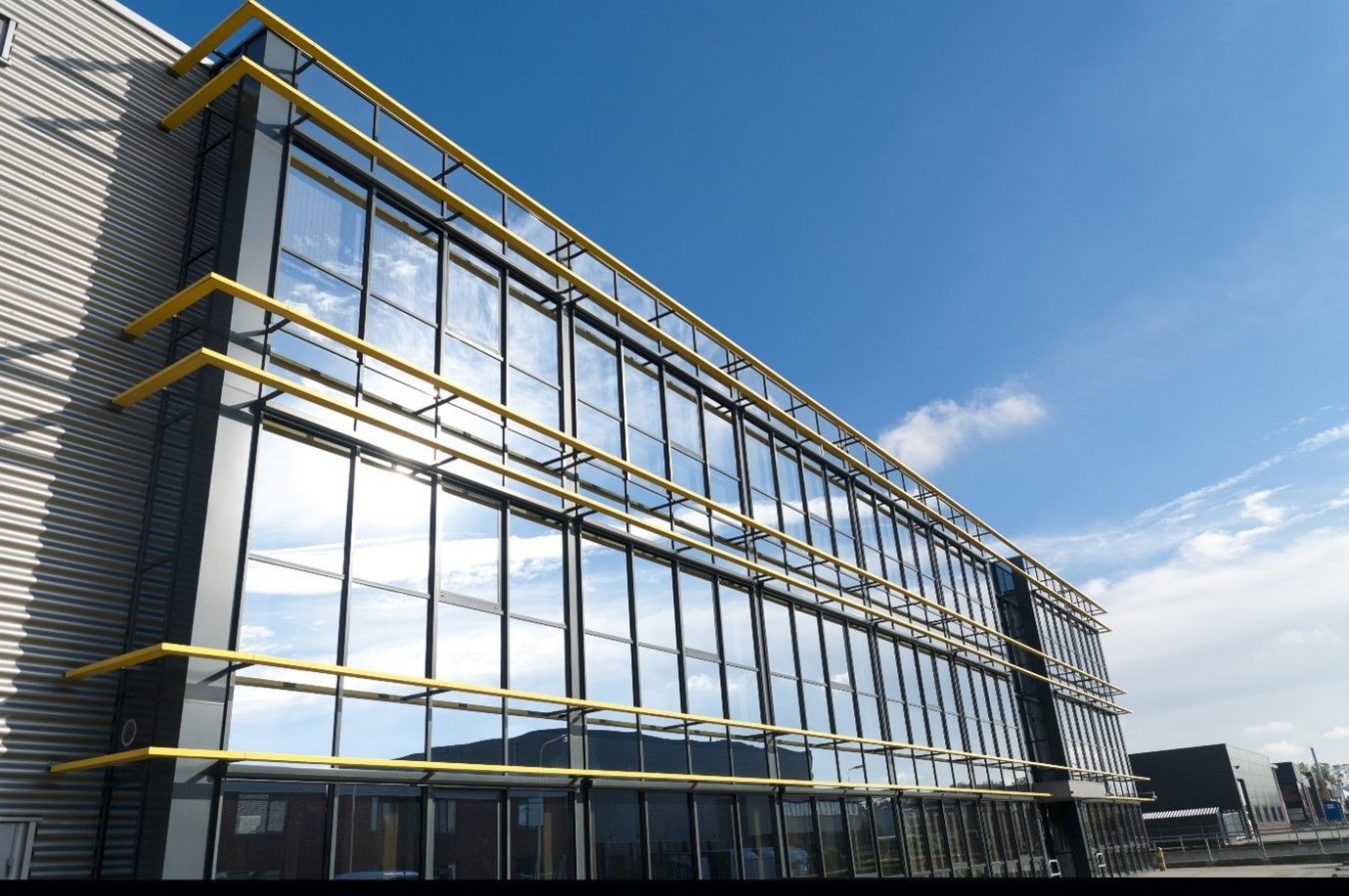